At KingStar, manufacturing premium stainless steel drinkware isn’t just about advanced machinery or premium materials. It’s fundamentally about people. That’s why ongoing employee training is one of our core business strategies. In an industry that constantly evolves—whether through customer expectations, global sustainability standards, or technological advancements—we understand the necessity of building a capable, adaptable, and skilled workforce.
With more than two decades of experience in OEM and ODM stainless steel drinkware manufacturing, KingStar has grown into a trusted supplier for global brands and retailers. Behind that success is a well-trained team that understands the mission and executes it with precision, creativity, and commitment.
Why Capability Building is Non-Negotiable in Precision Manufacturing
Capability building is more than just improving productivity—it’s about creating a culture of continuous improvement and innovation. Research has shown that organizations committed to developing their people outperform competitors by up to three times. At KingStar, we view training not as an occasional event, but as a continuous investment in our future.
By offering structured, targeted, and comprehensive training programs, we aim to empower every employee—from front-line machine operators to quality control inspectors—to take pride in their work and contribute meaningfully to our goals.
We approach training from four critical angles:
- Business Understanding – Helping our team understand KingStar’s mission, strategic priorities, and market position.
- Leadership and Management Skills – Equipping team leaders with the tools to manage efficiently and lead by example.
- Technical Mastery – Providing in-depth training on equipment, materials, and processes used in our stainless steel bottle manufacturing.
- Personal and Professional Development – Supporting personal growth and building soft skills that improve collaboration and performance.
Key Areas of Training at KingStar
To maintain our edge as a high-performance, globally competitive manufacturer, KingStar has implemented training across multiple key areas. Each program is tailored to meet both individual and organizational development goals.
1. Equipment Operation Training
Modern stainless steel vacuum bottle manufacturing relies on a range of sophisticated machines—from water expansion machines and vacuum sealers to polishing units and robotic welding systems. Every operator undergoes intensive, hands-on training. They don’t just learn buttons; they understand the machine’s mechanics, optimal operating parameters, common failure modes, and essential troubleshooting.
We believe that true mastery of equipment leads to fewer errors, smoother production flows, and less downtime. For example, our staff operating the water expansion machines must know not only how to initiate cycles, but also how to identify wear, troubleshoot common faults, and optimize output settings based on material specifications. This ensures not just operation, but mastery, minimizing downtime and maximizing yield.
Cross-training is also encouraged. In the event of employee absences, others are equipped to temporarily step in, ensuring continuous operation without disruption.
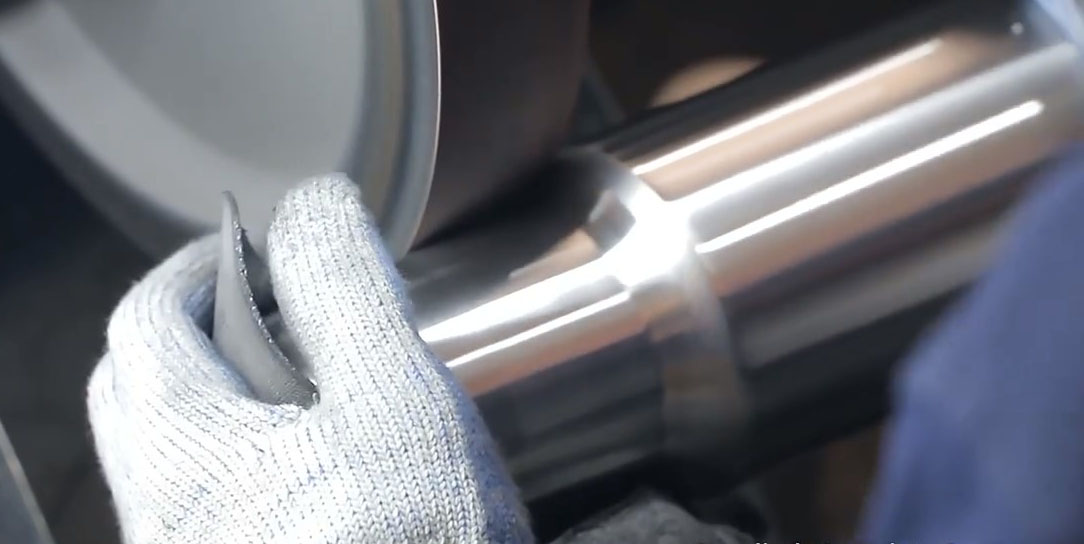
2. Safety and Compliance Training
“Zero tolerance for safety violations, no safety, no production.” In a metalworking environment with presses, high temperatures, chemicals, and moving machinery, safety isn’t just policy; it’s a sacred commitment. Safety training is conducted regularly, especially for new hires and staff working directly with heat, high-pressure machinery, or sharp tools.
- Routine, Scenario-Based Drills: Training goes beyond manuals. We conduct regular, realistic drills covering machine guarding, lockout/tagout procedures, chemical handling (powder coatings, electrolytes), and emergency response.
- Intensive Fire Safety Focus: Given the potential hazards in a manufacturing setting, fire prevention and response training is paramount. We utilize real-world case studies to vividly illustrate risks, teach meticulous housekeeping, ensure proper flammable material storage, and drill evacuation procedures until they become instinctive. Employees learn not just what to do, but why specific precautions are non-negotiable.
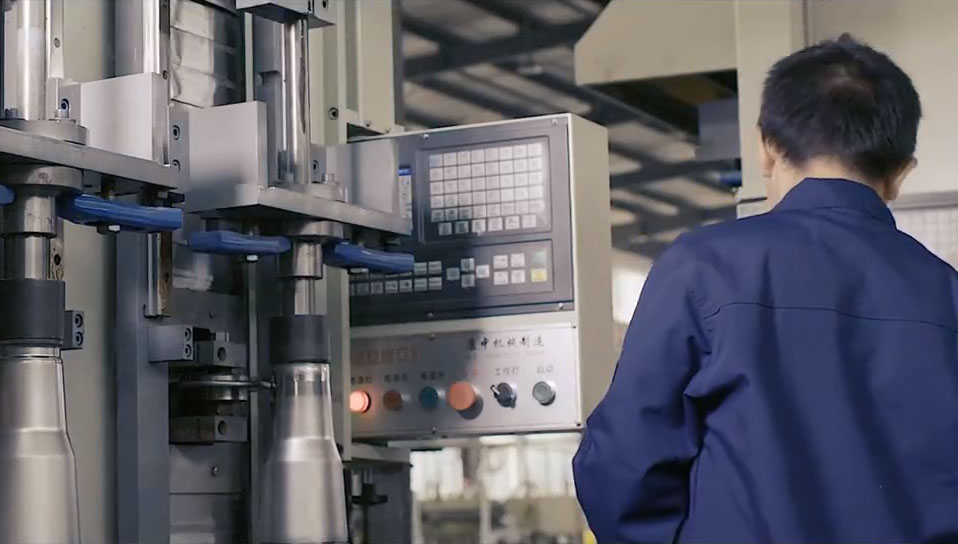
3. Quality Assurance Training
In the world of stainless steel water bottles, quality isn’t a luxury—it’s a necessity. Every bottle we produce, whether for outdoor adventure brands or corporate gifts, must meet strict durability and insulation performance standards.
Through quality training programs, our employees gain an in-depth understanding of:
- International quality standards like RoHS, FDA, LFGB, and Prop65
- Product inspection techniques across production stages
- Tolerance thresholds and defect identification
- The importance of clean, even powder coating and logo durability
By embedding “quality consciousness” into our workforce, we reduce waste, minimize rework, and ensure our clients receive premium-grade products every time.
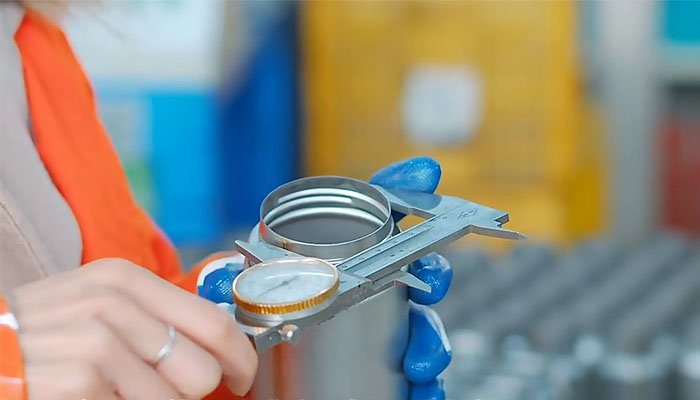
4. Basic Knowledge & Industry Awareness
Whether it’s understanding why 18/8 stainless steel is used in insulated tumblers, how heat retention works in vacuum-sealed bottles, or how to identify surface defects, having the right knowledge base improves decision-making on the floor.
Employees are trained on a wide range of topics, including:
- Types of stainless steel and their applications
- Thermal insulation principles
- Surface coating techniques (e.g., powder coating, spray painting)
- Differences between screen printing, laser engraving, and transfer printing
We also encourage staff to stay curious. With regular internal workshops and optional learning sessions, our employees continuously build their skill set and stay ahead of market demands.
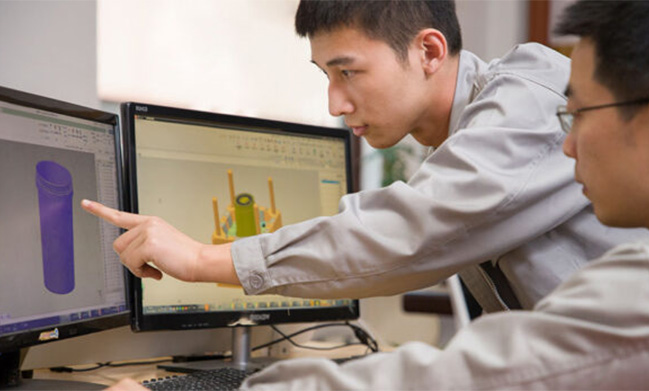
5. Improving & Innovation Design Capabilities
At KingStar, innovation is more than just a buzzword—it’s part of our DNA. That’s why we put a strong focus on strengthening the design capabilities of our R&D team, engineers, and product developers.
To support this, we provide targeted training programs in areas such as:
- CAD and 3D Design Software Mastery – Ensuring our team can quickly and accurately render custom shapes, lids, and components for tumblers, mugs, and bottles.
- Materials Innovation Workshops – Keeping our teams updated on the latest advancements in stainless steel alloys, coating technologies, and eco-friendly components.
- Process Automation Training – Teaching staff how to integrate new design ideas into automated manufacturing systems, from smart molds to robotic finishing processes.
- Market Trend Immersion – Design and technical leaders participate in sessions analyzing global drinkware trends – the rise of smart bottles with hydration tracking, demand for unique ergonomic shapes, integration with app ecosystems, sustainability drivers, and evolving customization desires. This ensures our innovation pipeline remains relevant and proactive, allowing us to anticipate and meet partner demands effectively.
Results We’ve Seen
Since implementing more structured training at KingStar, we’ve noticed measurable improvements in:
- Production efficiency: Reduced downtime and quicker shift transitions.
- Product quality: Fewer reworks and consistent results across batches.
- Workplace morale: Employees report feeling more confident and valued.
- Customer satisfaction: Fewer issues post-shipment and more positive feedback on product consistency.
In turn, these improvements help us maintain short lead times, meet low-MOQ requests, and deliver the kind of flexibility wholesalers and retailers appreciate.
Above all, employee training is a cornerstone of our success at KingStar. It ensures our stainless steel water bottles, tumblers, and mugs continue to set the bar for quality, safety, and innovation. More importantly, it builds a culture of continuous growth—where everyone from welders to engineers contributes to making our products better every day. For more information, feel free to contact us through our online messaging system or by emailing us at sales@waterbottle.tech. We guarantee a prompt response within 24 hours.