How to design vacuum flasks that can be manufactured? How to design vacuum insulated stainless steel water bottles with excellent thermal insulation performance, durable and stylish? This is a huge challenge faced by many designers.
The double-wall stainless steel vacuum insulated water bottle is different from the single-wall stainless steel water bottle. The existence of the vacuum layer between the inner and outer walls makes the design more difficult. Most of the design drawings sent to KingStar have unreasonable designs, and even using KingStar’s most advanced manufacturing technology and manufacturing equipment in the world is still difficult to fabricate. In many cases, the particularity of the vacuum insulation layer is not considered by designers. From manufacturing point of view, the wall thickness, wall gap and overall feasibility in those design drawings need to be modified. In order to save designers’ time, KingStar R&D team has summarized the following considerations and suggestions:
-
The distance between the inner and outer walls
Space at bottle body: The distance between the inner wall and the outer wall is usually 3mm, and the minimum is 2mm. There must be a vacuum layer with enough space to achieve the thermal insulation effect;
Space at bottle bottom: The distance between the inner and outer walls of the vacuum layer at the bottom of the vacuum flask is usually 10mm, and the minimum is not less than ≥8mm. If the distance between the bottom vacuum layer is too small, after vacuuming, under the action of air pressure, the bottom of the outer wall will deform and then touch To the bottom of the inner wall.
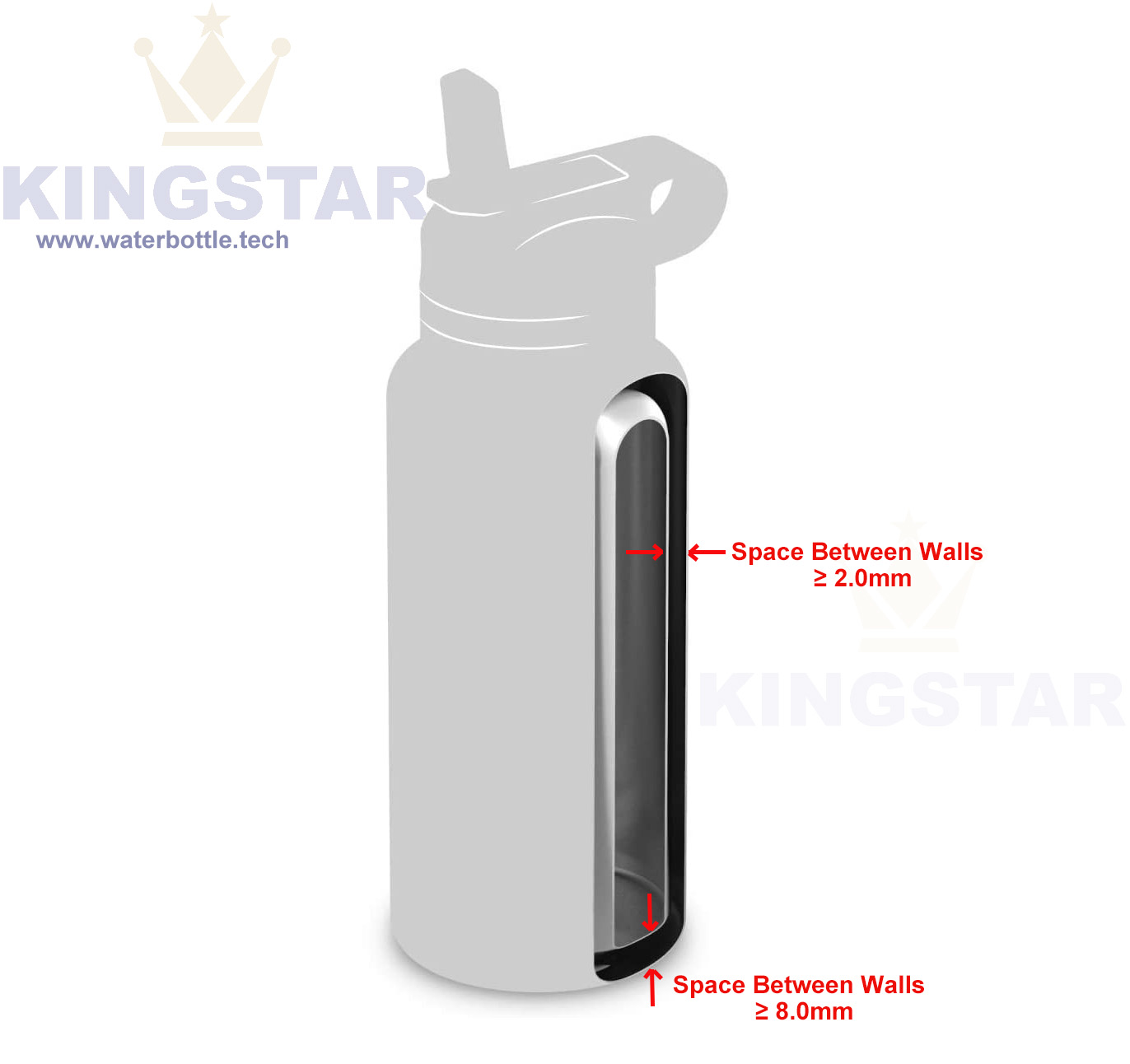
space between vacuum flask inner and outer walls
-
Thread design
Because the threads on the stainless steel water bottle are made by roll threading, not by turning. Therefore, thread with small pitch or large height cannot be applied.
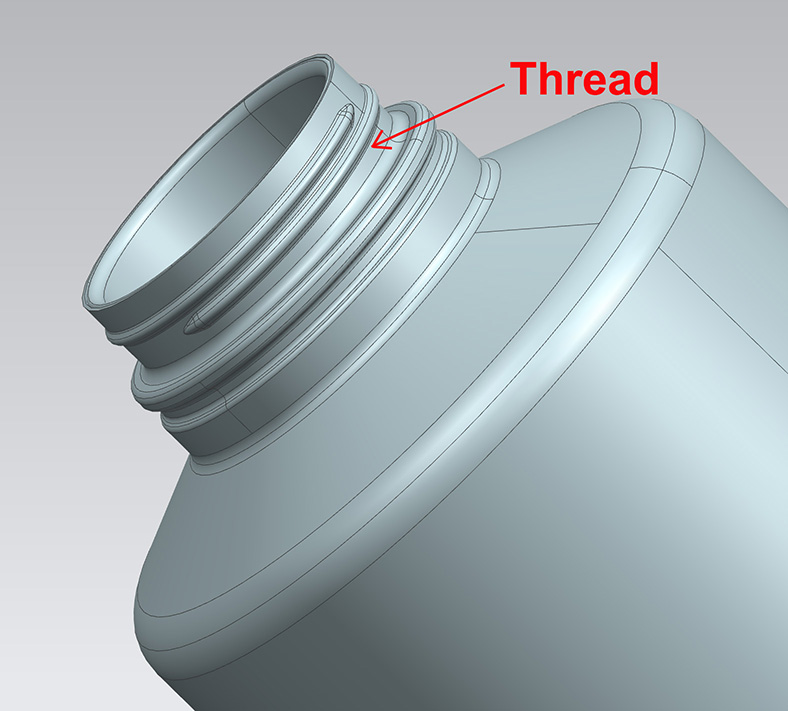
When designing the thread on the vacuum thermos flask, the designer needs to pay attention that:
Height of thread: The height of thread cannot greater than 1.0 mm. It is reasonable for the thread height to be between 0.5-0.9mm. Thread height lower than 0.5mm will cause slippage.
Regarding the thread design on the lid, the height of the thread must be less than 1.2mm.
Pitch of thread: The lower limit of the pitch is 3mm. The pitch of thread on the insulation bottles is usually between 4mm-5mm. When the pitch is less than 3mm, the defect rate in the production process will be very high, and the reliability of the product will be reduced, and the life of the thread will be shortened.
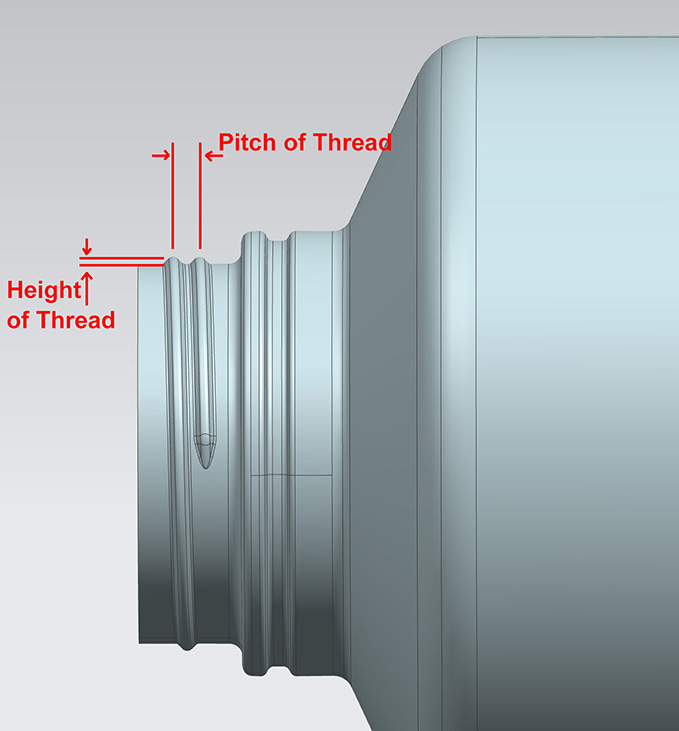
thread limit on vacuum insulated stainless steel water bottles
roll threading process of thermos water bottle manufacturing
Click here to know more about Manufacturing Process of Vacuum Insulated Stainless Steel Bottles
-
The thickness of the inner and outer stainless steel walls
When the diameter of the insulated water bottle is less than 70mm, stainless steel with a thickness of 0.4mm is usually used; For the diameter of the insulated water bottle larger than 70mm, stainless steel with a thickness of 0.5mm, 0.6mm, or 0.7mm is used according to actual needs. The thicker the stainless steel, the more durable, but the higher the cost.
-
Restrictions on the appearance and shape of the vacuum flask (Can KingStar make a square, rectangular or oval vacuum flask?)
The overall appearance of the thermal insulation cup is usually round. The cup body is generally shaped by water expanding process or a stamping process. As a leading stainless steel water bottle OEM manufacturer, KingStar can manufacture rectangular and angular vacuum flasks / water bottles / food containers / tumblers / vessels / drinkware, but the main reason why KingStar did not manufacture square and rectangular vacuum flasks in large quantities is:
- Air pressure causes the body of the rectangular vacuum flask to deform.

KingStar vacuum insulated stainless steel square drink bottle
After years of painstaking research and development, KingStar has rich experience in manufacturing small-capacity and reasonable-weight rectangular vacuum flask. If a large-capacity and large-size square insulation vessel is to be manufactured, the thickness of the inner and outer walls must be significantly thickened, otherwise, under the pressure of air, the inner and outer walls will deform and fit together. The result of this is that the cost increases, the unit price increases, and the weight of the cup body also increases significantly.
Why should vacuum insulated stainless steel vessels be round?
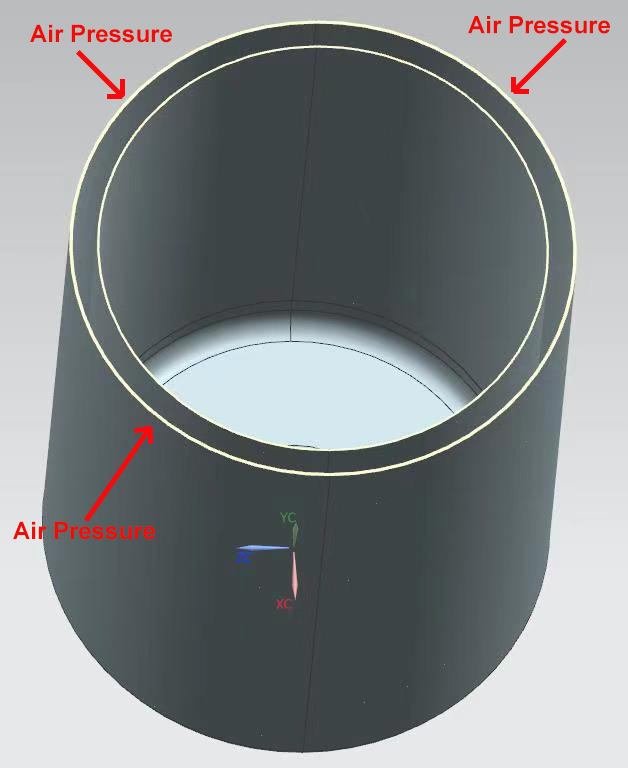
vacuum flask cross section
After vacuuming the space between inner and outer walls of the thermos cup, every point of the thermos cup bears even and huge air pressure. In this case, the circular structure is the most stable and performs best. This principle is equivalent to the arch bridge built in ancient times. Those arch bridges have not collapsed for hundreds of years without reinforced concrete, which is the use of the mechanical structure characteristics of arch bridges.
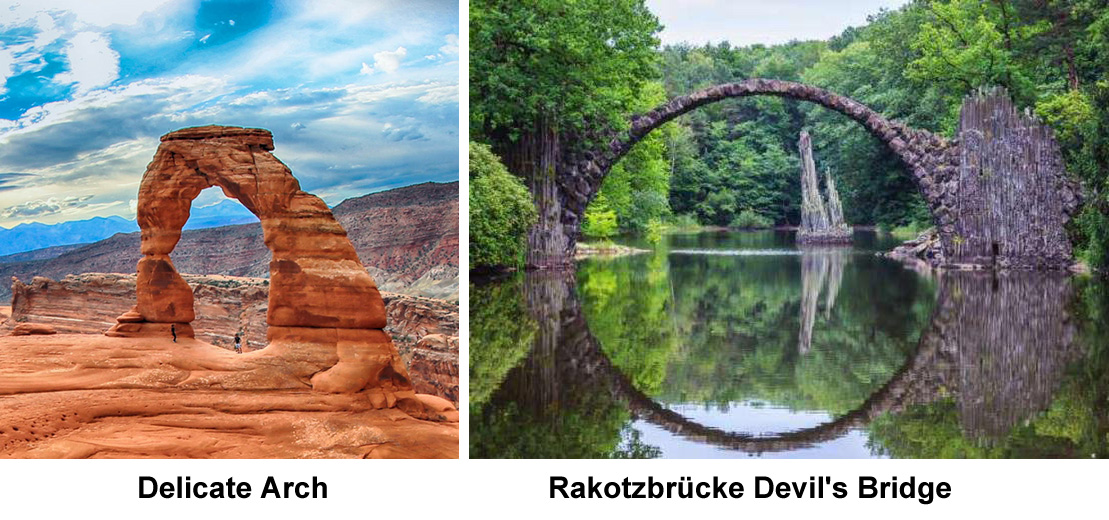
arch bridges
-
How to design to make the thermal insulation performance better
- Minimize the diameter of the bottle mouth
- Use stopper to reduce heat conduction from the mouth of the cup.
- Do copper plating to the outer side of the inner wall. Click here to read more about copper plating process.
- Wrap the aluminum foil on the outer side of the inner wall of the vacuum insulated bottle tumbler, but this cost is higher, and it will increase the space between the inner and outer walls, resulting in a significant increase in the size of the metal water bottle.
- Appropriately increase the capacity. Comparing the vacuum flasks of the same capacity, the vacuum flasks with larger capacity has better heat preservation effect and the temperature changes more slowly.
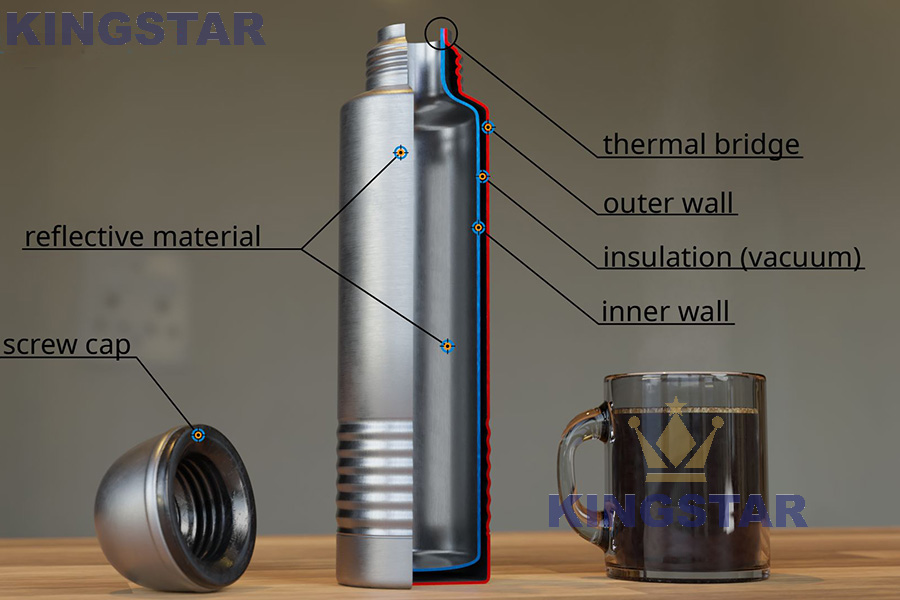
-
The location of the vacuuming point
The vacuuming point is usually set at the center of the bottom of the vacuum insulated water bottle. Before vacuuming, it is necessary to punch a hole in the center of the outer wall of the bottom, and vacuum from the position of the hole. The point where the hole is punched is the vacuuming point. The location of the vacuuming point at the bottom does not affect the appearance of the entire product. Vacuuming at the center of the bottom, so that the air force on the bottom is more even, and the bottom of the bottle will not be deformed due to strong suction.
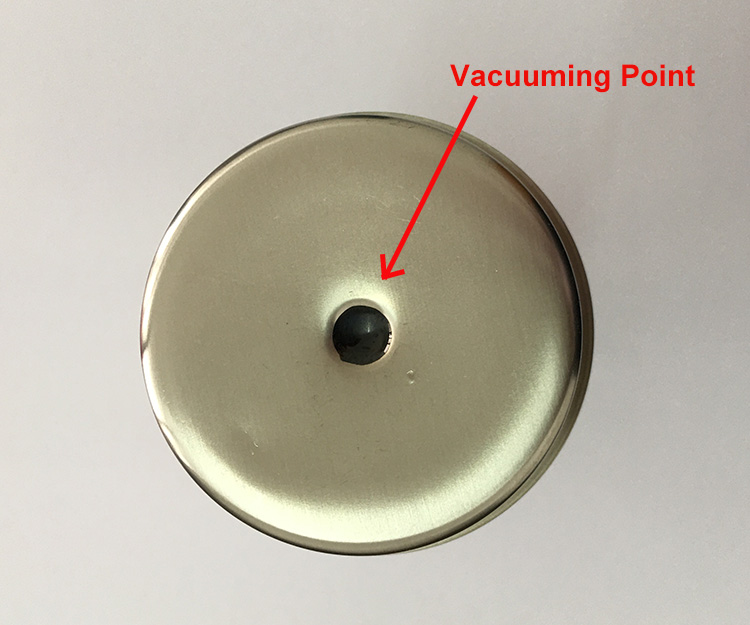
vacuuming point on insulated water bottle
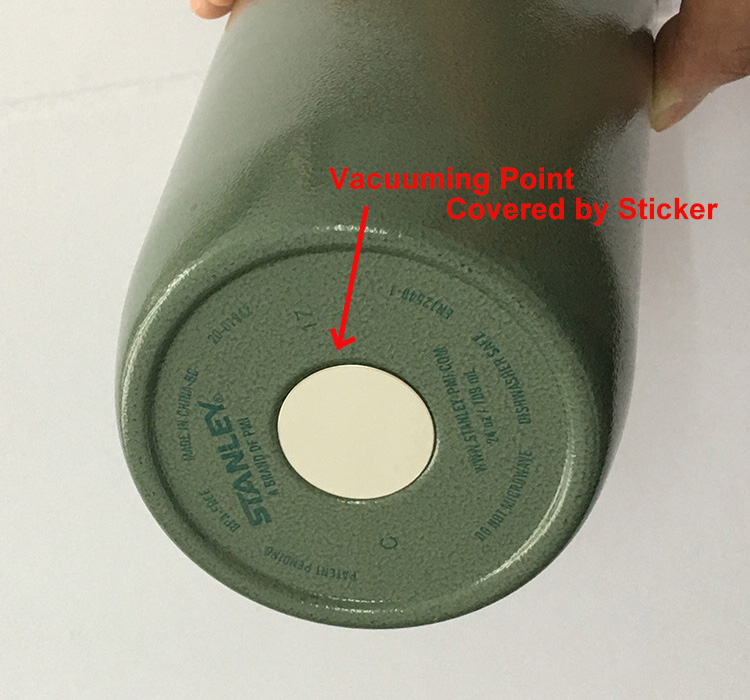
vacuuming point covered by sticker
-
Design of silicone seal gasket
Generally, there are two types of sealing design, side sealing and top sealing. Side sealing is usually used for pressed-in lids (such as tumbler lids). Top sealing is as cola shaped bottle lid.
Normally, the thickness of the silicone silicon ring on the side sealing is 1mm; The thickness of the silicone ring for top sealing is 2-3mm.
-
Selection of metal material for bottle
The materials of thermos cups are mostly 18/8 stainless steel (SUS304 stainless steel) and 201 stainless steel. Because 201 stainless steel is harmful to the human body, 201 stainless steel cannot be used for the inner wall of the vacuum flask. The water bottle made of 201 stainless steel can’t pass the FDA test.
For thermal insulation containers used in medical equipment items, or thermal insulation containers related to medical treatment, they need to be made of 316 stainless steel.
For more articles about materials, please refer to the following links:
18/8 Stainless Steel (SUS304): The Best Material for Making Vacuum Flasks
316 and 304 Stainless Steel: a Far More ECO Friendly Water Bottle Material
-
Selection of plastic material for lid/cap
Most of the lid materials are PP, Tritan and AS, all of which are BPA free.
KingStar can use Recycled plastic such as Ocean Plastic to make the lids of the water bottles. Since the quality of this type of material is difficult to control, if the customer specifies to use recycled plastic, we hope that the customer can provide the raw material, or specify the supplier of the raw material.
Click here to read more about Design Process of Injection Mold for Custom Water Bottle Lid
KingStar R&D team provides design services. You just need to tell us your design idea or sketch, we will make 3D drawings accordingly, and make a 3D printed prototype and submit it to you for confirmation.
Need help to design vacuum insulated double walled stainless steel water bottles? Need an exclusive manufacturer factory to make your custom design water bottles? Please just contact us any time.