Contents
- The Complex Structure of Injection Molding
- Guidance system
- Supporting system
- Molding system
- Gating system
- Cooling system
- Ejection system
- Exhaust system
- The Cost Structure of Bottle Tumbler Injection Mold Tooling
- How to Reduce the Injection Molding Cost of the Cup Lids
- The Difference Between Injection Molding of Bottle Lids and the Stamping Tooling of the Bottle Body
- How Much Does It Cost to Develop Mold Tooling for New Water Bottle Project
Our customers, particularly those who are about to develop custom shape drinkware such as water bottle, drinking cup, tumbler, mug, lunch box, insulated bowl and stainless steel vessel, have asked us the question many times about why the mold of such plastic components as plastic lids and handles are quite costly, while the mold for producing the container part of the stainless steel cup is relatively cheap.
It is well known that “Mold is the mother of industry” and the importance of mold has increasingly been recognized. Nowadays, water bottle manufacturers have made huge strides in mold designing and water bottle manufacturing technology. As the top metal water bottle manufacturer, Kingstar is committed to providing innovative design of mold manufacturing technology and applying all sorts of new mold materials in an attempt to spend more time on mold designing and cut the cost.
Water bottle plastic components like the lid and handle are typically made by complex and high-precision injection mold. Injection molding is a sophisticated process which normally includes the following seven systems: guidance system, supporting system, molding system, gating system, cooling system, ejection system, and exhaust system.
The manufacturing of the container part of the stainless steel cups relies on molds as well, and there are several main types as stamping mold tooling, stretching mold, calendaring mold and falling hammer dies. These molds have a simple structure and require quite harder materials. Here we are going to introduce the structure of injection molding for lids and its cost, how to reduce its cost and the difference between injection molding of lids and the stamping die of the cup.
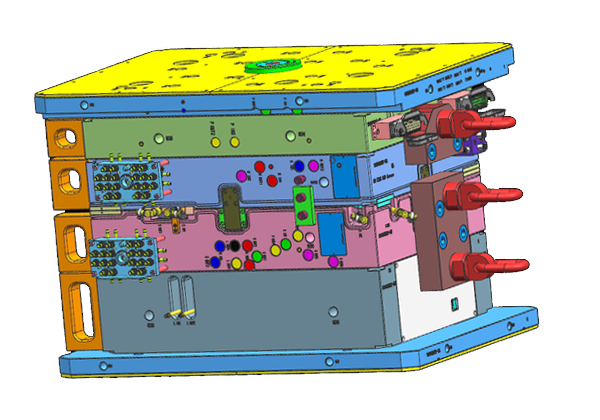
The Complex Structure of Injection Molding
The injection molding consists of seven systems: guidance system, supporting system, molding system, gating system, cooling system, ejection system and exhaust system. All these systems together create a mold and it requires several steps to finish a molding cycle: first pour the plastic liquid through the nozzle of the injection molding machine to the inside of the molding chamber, and keep the screw unchanged with the same pressure for several seconds after the injection, next let the cooling system do its work and the last step is to wait for the ejection system to push out the condensed components which is already being shaped.
-
Guidance system
This system is mainly used to promote the perfect collaboration between the two major parts-the male die and the cavity- and other components, aiming to make sure the precision of the shape and size of such plastic parts as bottle lids and handles and avoid the collision and interference between different parts inside the mold.
-
Supporting system
During the process when the mold is formed, the high pressure exerted on the plastic will cause the mold to change its form should the template is not hard enough. Thus the product will be made with a poor quality and display rough edges. Without increasing the thickness of the template, it is necessary to have a supporting component to improve the stiffness and hardness of the template helping overcome the deformation of it.
-
Molding system
This system is designed to successfully eject the finished and ideal products.
-
Gating system
It is the route that the plastic particles travel in the mold starting from the process when they are being melted and ejected from the nozzle of the injection molding machine to the cavity. The principles of such design is to speed up the formation and shorten the forming cycle as well as ensuring the quality of such plastic components as plastic cup lids and handles.
-
Cooling system
The cooling system includes several parts: the cooling channels, the mold temperature controller and heating element.
The role of cooling channels:
5.1. To control the temperature of the mold and improve the quality of the product in the aspects of its sheen, residual stress, crystallinity and hot bending.
5.2. To help reduce the molding cycle. The well-designed cooling system in the early stage is very necessary to improve efficiency because 80% of the molding cycle is for cooling.
5.3. To cool down some massive slidable parts in an attempt to avoid them being stuck during operation.
-
Ejection system
The ejection of the plastic components such as the plastic cup caps and handles are the final part of injection molding. It requires an effective approach to ejecting the plastic lids and handles from the mold after
they solidify.
-
Exhaust system
In addition to the existing air in the cavity, there is still water vapor produced by the water on the plastic that evaporates under the injection temperature, the volatile organic compounds of the low molecule weight caused by the partial overheating of the plastic and gases released by the plastic additives (or chemical reaction) and the solidification of thermosetting polymer. The exhaust system is designed to remove the gas because it affects not only the molding of the plastic lids and handles but also the quality of them after demolding.
The Cost Structure of Bottle Tumbler Injection Mold Tooling
The cost of injection molding for water bottles & tumblers refers to the design, raw materials manufacturing and so on.
The design cost also includes the upfront cost of communication. The design process compromises the CAE analysis, the design of the molding structure and 2D drawings.
The cost of raw materials includes some steel, standardized parts, hot runner and mold base used to make the moving die to form.
The manufacturing cost consists of processing, polishing, pilot production and the match between some components such as the cavity and the core as well as the slider and the runner.
The design cost accounts for about 5% of the processing cost, the raw materials about 30%-40% and the manufacturing about 30%-45%.
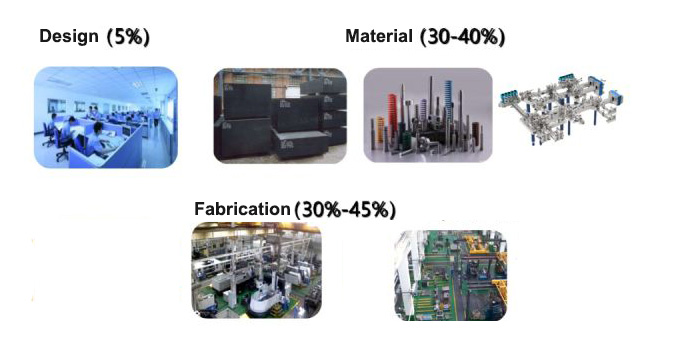
How to Reduce the Injection Molding Cost of the Cup Lids
- To cut down the numbers of components used on the plastic lids through optimizing the design.
- To simplify the shape of the plastic lids by optimizing the design.
- Typically, the more complicated the design of the components used on the lid, the more costly it is for the mold.
- To reduce the precision of the plastic mold. The precision and stiffness of the mold should be in line with the requirements of objective production standards and production programs. The higher the demand for the precision and stiffness, the more expensive the production cost is.
- To depreciate the mold life. A longer lifespan means that a mold can be injected for more times, which will also elevate the price of raw materials.
- To finish the design once and for all. Do not change the product design when the manufacturing of the mold is already in progress. The change of the design will inevitably lead to the change of the mold, which will result in the exorbitant cost of remolding.
The Difference Between Injection Molding of Bottle Lids and the Stamping Tooling of the Bottle Body
As a technology-intensive production, the stamping die is an indispensable tool for producing the container part of the vacuum cup. There’s a direct link between the design and manufacturing of the stamping die and the quality, efficiency and production cost of the stainless steel cup. The level of mold designing and manufacturing skills is one of the most important standards to measure the capability of a cup manufacturer. The absence of a heating system and cooling system makes it cheaper to design and produce with a stamping die.
Injection molding, also known as injection forming, has been widely used in manufacturing water bottles. The lid, handle, silicone pad and seal ring are all made by injection molding. The structure of injection molding is relatively complicated and more expensive compared with its counterparts.
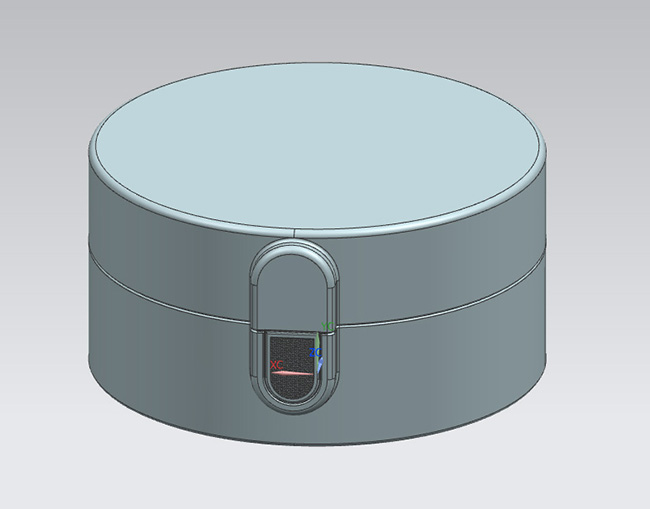
How Much Does It Cost to Develop Mold Tooling for New Water Bottle Project
Our clients, whether they are buyers from big brands or large companies, or small startups, or crowdfunding projects on KickStarter, Indiegogo, GoFundme or CircleUp, all want to know the mold fee at the beginning of the unique design bottle tumbler project. However, to quote an accurate mold fee, we need to do these 3 steps first:
- Review customer drawings
- Propose revisions to ensure that the product can be produced smoothly
- Client agrees to modify and approve 3D printing samples
After the above three steps are completed, KingStar’s engineers can quote the exact pricing.
Overall, the mold fee for a bottle cap is about $5,000-$15,000. The specific injection mold price depends on the complexity of the cover, the number of parts, the mold life requirements, etc.
The mold fee for the water bottle / cup body is about $2000-7000. The specific price of the cup body mold fee depends on the capacity of the water bottle cup, whether the cup body is double-layered insulation, and the shape of the cup body.