In the manufacturing of thermal insulated stainless steel bottles and cups, vacuum insulation is key to performance. This process creates a vacuum seal between the inner and outer layers of stainless steel, dramatically reducing heat transfer. However, achieving a durable and effective vacuum seal requires precise materials — particularly, the use of lead-free low-temperature solder.
This solder isn’t just a filler. It’s a finely engineered alloy with specific chemical properties that enable it to form robust seals under carefully controlled temperature conditions. It also needs to meet international safety and environmental regulations, such as RoHS and China’s SJ/T 11392-2009.
So, what’s inside this special solder? What roles do the different metals and trace elements play? And more specifically — what role does phosphorus oxide play, and in what concentration? As a leading insulated water bottle manufacturer, KingStar will show you the core chemistry and functionality of this critical material in this post.
Core Alloy Components
1. Tin (Sn)
Tin is the main building block of most lead-free solders. Typically accounting for over 90% by weight, tin is valued for its excellent wettability, ductility, and electrical conductivity. However, with a melting point of around 232°C, pure tin is too hot for many applications, so it’s blended with other metals to lower the melting temperature.
In vacuum applications, tin provides the structural matrix that holds all the other elements together, allowing the solder to flow smoothly and adhere well to stainless steel surfaces.
2. Silver (Ag)
Silver, used in concentrations between 2.5% and 6%, is a key additive. It increases the mechanical strength and thermal fatigue resistance of the alloy. For example, SAC305 (Sn96.5Ag3Cu0.5) is widely used in electronics due to its balanced performance, though its higher melting point (~217–220°C) limits its use in ultra-low-temperature scenarios. In vacuum-sealed thermal cups, silver-containing alloys like SAC are often modified with additional elements to reduce brittleness and improve interfacial stability.
3. Copper (Cu)
Copper (0.5–1.3%) is added to refine the microstructure, suppress the growth of brittle intermetallic compounds (e.g., Cu₆Sn₅), and improve thermal cycling reliability. Copper also lowers the melting point slightly and enhances wetting properties, which is critical for forming robust joints in vacuum environments.
4. Bismuth (Bi)
Bismuth (3–58%) is a primary component in ultra-low-temperature solders (e.g., Sn42Bi58, melting point ~138°C). It significantly reduces the alloy’s melting temperature, making it ideal for heat-sensitive applications. However, Bi-rich alloys are prone to brittleness, especially under mechanical stress or rapid cooling, which can compromise long-term reliability in vacuum-sealed structures. Recent advancements, such as Durafuse LT (a hybrid of Sn-In-Ag and Sn-Ag-Cu powders), address this by combining low-temperature melting (~175–185°C) with improved toughness.
5. Indium (In)
Indium is used in specialized low-temperature alloys (e.g., Sn-In-Ag) to further depress the melting point (e.g., In52Sn48 melts at ~118°C). While effective, indium is costly and less common in mass-produced thermal cups due to supply chain constraints.
6. Antimony (Sb)
Antimony (2.5–4%) is added to improve tensile strength and creep resistance. It also refines grain structure, reducing the risk of crack propagation under thermal stress. However, excessive Sb can reduce ductility, requiring careful balancing with other elements.
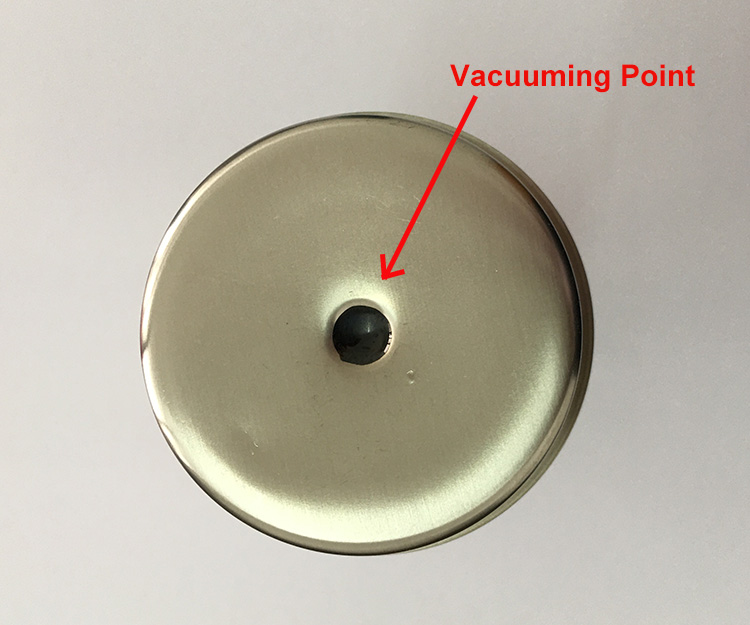
Click and read more about Custom Options: Custom Bottle Tumbler Decorating, Custom Logos of Water Bottles, Custom Water bottle Packaging
Trace Additives and the Role of Phosphorus Oxide
1. Phosphorus (P) and Phosphorus Oxide (P₂O₅)
Phosphorus is incorporated in minute quantities (0.0001–1%) as a deoxidizer and wetting agent. It prevents oxidation during the soldering process and enhances the flow characteristics of molten solder. In some formulations, phosphorus is introduced as phosphorus oxide (P₂O₅) or through phosphorus-containing intermediates (e.g., during alloy preparation).
Role of Phosphorus:
- Reduces surface tension of the molten alloy, improving wettability on stainless steel substrates.
- Inhibits the formation of undesirable oxides (e.g., SnO₂), which can weaken joints.
- Stabilizes the alloy’s microstructure by suppressing excessive intermetallic growth at the solder-substrate interface.
Typical Concentration:
Phosphorus content in lead-free solders for vacuum applications is tightly controlled. For example, patents describe formulations with 0.0001–1% phosphorus (or equivalent phosphorus oxide). Higher concentrations (>1%) may lead to brittleness or interfacial voids, while insufficient phosphorus (<0.0001%) compromises oxidation resistance.
2. Rare Earth Elements (REEs)
Elements like neodymium (Nd), yttrium (Y), and cerium (Ce) (0.02–0.5%) are added to refine grain structure, enhance mechanical properties, and stabilize interfacial compounds (e.g., preventing Cu₆Sn₅ → Cu₃Sn transformation). These elements are particularly effective in high-reliability applications, such as aerospace or automotive electronics, which share similar demands with vacuum-sealed thermal cups.
3. Nickel (Ni) and Manganese (Mn)
Nickel (0–0.05%) and manganese (0–0.1%) are used to inhibit the coarsening of intermetallic layers and improve high-temperature stability. Manganese also enhances toughness in Bi-containing alloys, mitigating their inherent brittleness.
Typical Alloy Systems and Compatibility with Vacuum Processes
Here are some representative lead-free low-temperature solder formulations used in vacuum insulation applications:
Alloy Type | Typical Composition | Melting Range | Characteristics | Vacuum Process Compatibility |
---|---|---|---|---|
Sn-Bi System | Sn42Bi58 | 138°C | Ultra-low temperature, low cost, but high risk of brittleness | Requires rare earth (RE) or antimony (Sb) to improve toughness |
SAC System | Sn96.5Ag3Cu0.5 (SAC305) | 217–220°C | High strength, high reliability | Suitable for high-temperature vacuum furnace processes; inert gas shielding recommended |
Sn-Ag-Cu-P | Sn-Ag3-Cu0.7-P0.05 | 200–215°C | Low oxidation, excellent wettability | Ideal for flux-free vacuum soldering |
Sn-Bi-Sb-RE | Sn40Bi55Sb3Nd0.2 | 140–145°C | Low-temperature, high toughness, thermal fatigue resistance | Directly applicable to vacuum sealing without post-processing |
Key Notes:
1. Abbreviations:
- SAC: Tin-Silver-Copper (Sn-Ag-Cu)
- RE: Rare Earth elements (e.g., Nd, Y, Ce).
2. Compatibility Focus:
- Sn-Bi Systems: Prioritize ultra-low temperature but require toughness modifiers (e.g., Sb, RE).
- SAC Systems: Balance strength and reliability, often used with inert gas protection to prevent oxidation.
- Sn-Ag-Cu-P: Optimized for minimal oxidation, suitable for flux-free vacuum environments.
- Sn-Bi-Sb-RE: Engineered for direct vacuum sealing with enhanced thermal-mechanical stability.
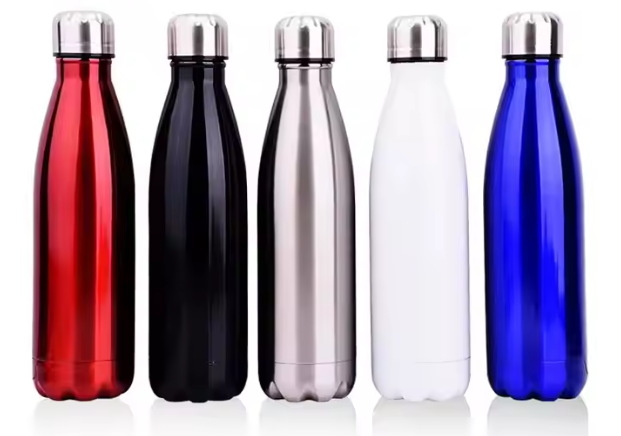
Challenges and Solutions in Vacuum Soldering
1. Volatility of Bismuth
Issue: High-Bi alloys (e.g., Sn-Bi) may volatilize under vacuum, leading to porosity or joint weakening.
Solution:
- Using Bi in lower concentrations (3–3.5%) with Sb or REEs to stabilize the microstructure.
- Employing inert gas shielding during soldering to minimize vaporization.
2. Oxidation Control
Issue: Phosphorus and rare earth elements are critical for reducing oxide formation.
Solution: Fluxless soldering techniques are often preferred in vacuum processes, relying on alloy self-cleaning properties.
3. Interfacial Stability
Issue: Excessive Cu₆Sn₅ growth at the solder-stainless steel interface can cause brittleness.
Solution: Adding Ni or Mn suppresses this by forming more stable compounds (e.g., (Cu,Ni)₆Sn₅).
Industry Standards and Safety
Lead-free solders for thermal cups must comply with standards such as SJ/T 11392-2009 (China) and RoHS. Key requirements include:
- Lead content ≤0.1%.
- Phosphorus and other additives within specified limits to ensure food safety (e.g., no heavy metal leaching).
- Compatibility with stainless steel (304/316 grades) to prevent corrosion or toxic metal release.
Summary
The solder used in vacuum-insulated stainless steel bottles, coffee cups, tumblers, mugs, shaker bottles, water jugs, can coolers, lunch boxes, coffee pots, beer growlers and hip flasks is more than just a melting filler — it’s a precisely engineered alloy that ensures air-tight sealing, thermal durability, and long-term safety. The core elements — tin, silver, copper, bismuth, indium, and antimony — are carefully balanced to achieve low melting points, strength, and wettability. Meanwhile, trace additives like phosphorus oxide (0.0001–1%), rare earth elements, and nickel play a crucial role in oxidation resistance and microstructure control.
Understanding the science behind these solders enables manufacturers to choose the best materials for reliable, long-lasting thermal products.
Want to get more information on water bottle manufacturing or bring your custom design drinkware into market, feel free to send us a message online or reach out via email at sales@waterbottle.tech. We respond within 24 hours.