Hydro Flask, a household water bottle brand in the United States, was one of the earliest companies that sold premium quality cold-retaining stainless steel water bottles in the market. Nowadays, Hydro Flask has released many new categories such as Outdoor, Kitchen, Beer & Wine and Food. The Hydro Flask water bottles are made of stainless steel SUS 304 with strong insulation performance, they can keep ice cubes cold for 24 hours or piping hot water warm for 6 hours, enabling customers to enjoy their favorite drinking anytime and anywhere.
What Materials Are Adopted To Make Hydro Flask Water Bottles?
Hydro Flask water bottles are made of optimal food grade, BPA-free and toxin-free materials. They are compliant with major standards such as FDA standards. The material information of each part of a Hydro Flask water bottle is listed as follows:
Bottle Body: Stainless Steel SUS 304 (18-8)
Bottle Lid/Cap: BPA-free Plastic
Seal Gasket: Solid Silicone
Flex Boot: Premium Silicone
(The flex boot is purchased separately.)
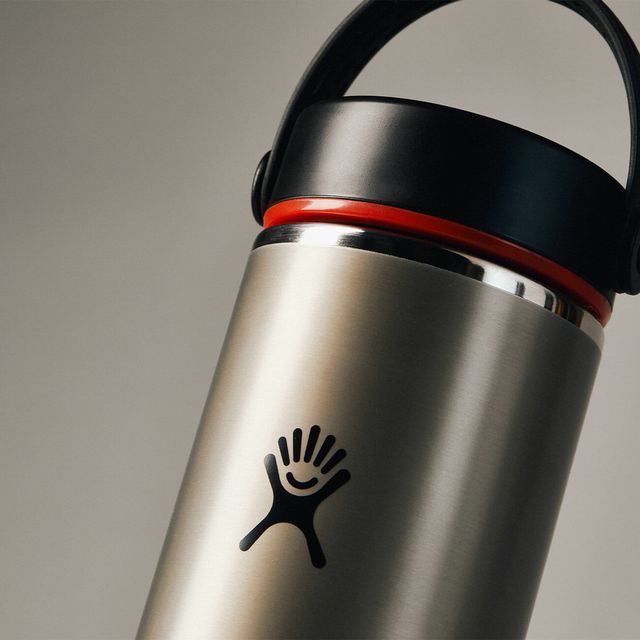
Click here to know more about Food Grade 18/8 Stainless Steel
stainless steel water bottle manufacturing video
Vacuum Insulated Stainless Steel Bottle Tumbler Manufacturing Process
Brief description: Stainless steel arrives at the factory in the form of pines and sheets –> Produce outer bottle and inner bottle –> Assembly and welding –> Vacuuming –> Decorating.
1. Manufacture Outer Bottle
1.1 Pipe cutting: Cut raw material – stainless steel pipe – to the appropriate length.
1.2 Expansion
There are basically two different ways to make stainless steel into the shape of a bottle: water expansion and stretching.
Water Expansion: Stainless steel pipes are raw material for this method. First, stainless steel pipe is put on the water expansion machine. The pipe swells into a bottle shape under the huge pressure of the water. With this method, the bottle formed is with no bottom, so a round stainless steel plate will be welded onto it to form a complete bottle.
Stretch: Stainless steel sheets are raw material for this method. First, the stainless steel sheets are cut into round plates at appropriate size, and then we use a punch press to stretch the stainless steel plate into a cylinder with a bottom.
The outer bottle can be formed by any of these two methods. Water expansion is more popular.
1.3 Separating: If using water expansion process to form outer bottle, then separating process is a must.
1.4 Shaping: Use a large press and follow the “Bottle Shaping Guide” to ensure that the pits, size and shape of the outer bottle meet the requirements.
1.5 Necking: Use a machine to squeeze the upside of the bottle to be a bottle neck.
1.6 Thread Rolling/Making: Threads are made with a special threading machine. Ensure that the thread meets requirements.
1.7 Cleaning: Removes lubricating oil and dust during molding.
1.8 Inspection
2. Manufacture Inner Bottle
2.1 Pipe cutting: Cut raw material – stainless steel pipe – to the appropriate length.
2.2 Expansion. Water expansion or stretch. The inner bottle can be formed by any of these two methods. Water expansion is more popular.
2.3 Separating
2.4 Shaping
2.5 Necking
2.6 Thread Rolling/Making (Normally if outer bottle is designed with thread, there’s no thread on inner bottle)
2.7 Cleaning
2.8 Inspection
3. Assembly (Bottle Mouth Matching)
Assemble the inner bottle and the outer bottle together by pressing machine.
4. Bottle Bottom Assembly
Assemble the bottom to the bottle by pressing machine.
5. Assembly (Bottle Mouth Welding)
Weld the inner bottle and outer bottle together to prepare for vacuum insulation. Ensure smoothness, no bumps or solder joints.
6. Assembly (Bottle Bottom Welding)
Weld the outer bottle and the bottle bottom to prepare for vacuum insulation. Ensure smoothness, no bumps or solder joints.
7. Leaking Test
Check whether inner bottle and outer bottle were well welded.
8. Vacuuming
Vacuuming with a vacuum machine.
9. Temperature Test / Insulation Test
Blow hot air into each bottle. If the outside of the bottle is kept cool, it means that the heat from the hot air will not be diverted and the bottle is vacuum insulated. On the contrary, if the bottle gets hot, there is a problem with vacuum insulation.
10. Electrolysis Polishing
Through the interaction of current and electrolyte to improve the micro-geometry of the metal surface, reduce the surface roughness of the metal, so as to achieve the purpose of bright and smooth surface of the stainless steel bottle. Surface of inner bottle to be bright and even, no watermark, yellow dot.
11. Mechanical Polishing
Polish the surface of outer bottle to ensure it is smooth and bottle mouth is smooth and bright. There must be no obvious drawing, scratching, black wire and pits.
12. Cleaning
Clean the bottle and dry it. Make the bottle ready for external coating / decorating.
13. Temperature Test / Insulation Test
Blow hot air into each bottle. If the outside of the bottle is kept cool, it means that the heat from the hot air will not be diverted and the bottle is vacuum insulated. On the contrary, if the bottle gets hot, there is a problem with vacuum insulation.
14. External Coating(surface decorating)
The bottle is now ready for external coating –powder coating or spray painting. KingStar is capable of doing both spray printing and powder coating process.
15. Pattern and Logo Printing
Print the pattern design and logo on the bottle with various techniques – screen printing, thermal transfer printing, water transfer printing, laser etching and so on.
16. Temperature Test / Insulation Test
Blow hot air into each bottle. If the outside of the bottle is kept cool, it means that the heat from the hot air will not be diverted and the bottle is vacuum insulated. On the contrary, if the bottle gets hot, there is a problem with vacuum insulation.
17. Packing
After inspect each bottle, including visual inspection and lid leak test, the bottle is place in a separate bag for packaging.
How Does The Hydro Flask Water Bottle Keep Beverages Cold/Hot?
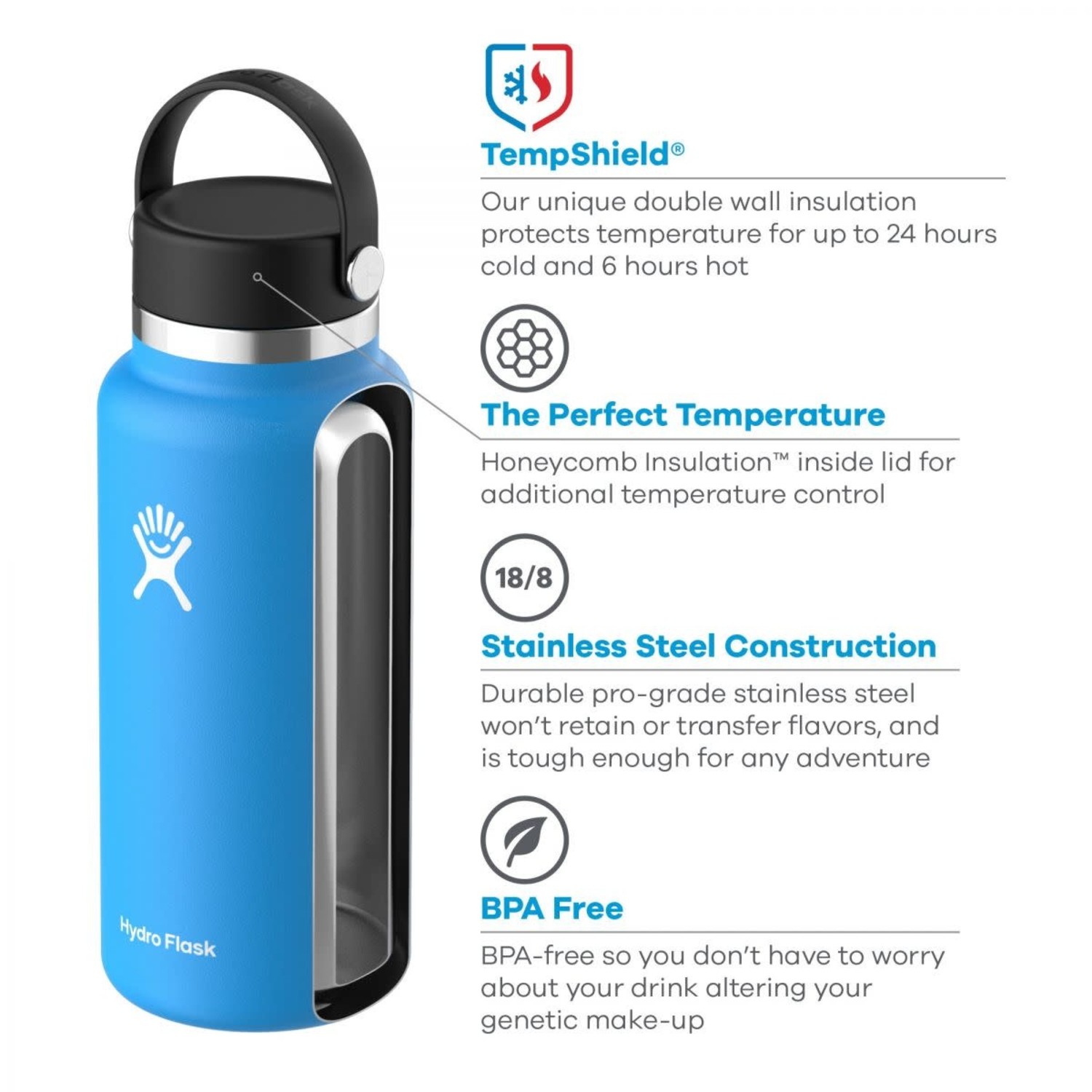
The Hydro Flask water bottle creates TempShield, a technology that adopts unique double-walled insulation structure, to realize the perfect cold retaining performance. A Hydro Flask water bottle can amazingly keep cold beverages cold for up to 24 hours, so you can take this compact and portable small refrigerator anywhere you like. Whether you are on the beach or at the sauna room, the water can be remained cold for your hydration. Besides, the vacuum layer between the double stainless steel walls also plays a vital role in preventing the heat from transferring through conduction and radiation. The reflective lining of the wall can reflect the radiation back, further sealing the heat inside of the bottle. The Hydro Flask water bottle, apart from adopting TempShield technology, also devises Honeycomb insulation and uses it in the lid/cap. In this way, additional temperature control is achieved, and this unique design is also welcomed by both customers and investors.
The Hydro Flask water bottle is applicable for holding ice cubes and hot drinks. Although this bottle is not expert at remaining hot temperature, its cold retaining performance dwarfs other water brands in the market. Water bottles of Hydro Flask also feature anti-rust and anti-scratch powder coating, which comes in a variety of fashionable colors and is also partly the reason why it appeals to so many students in colleges.
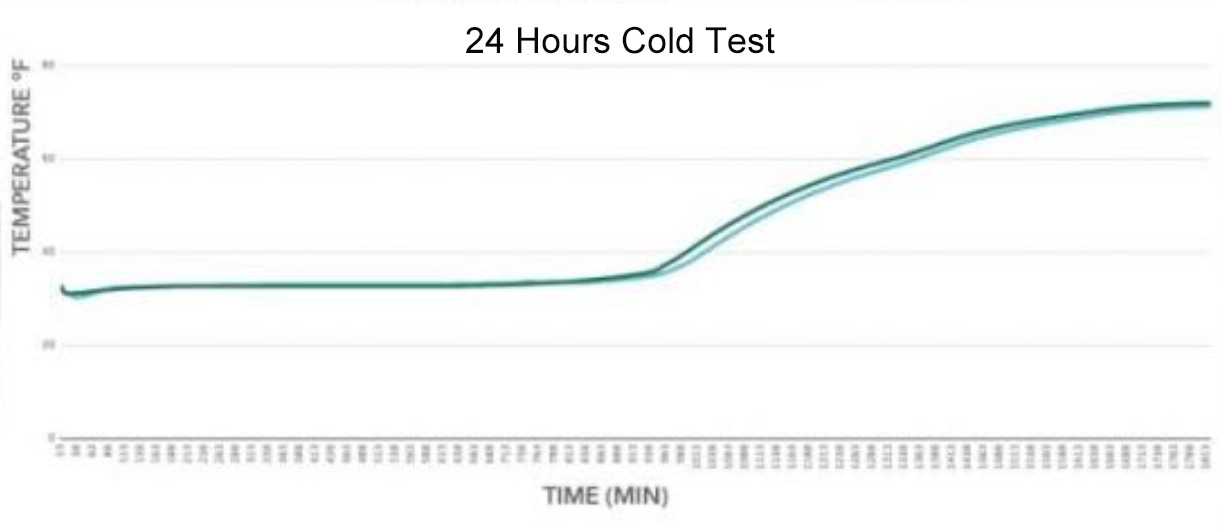
Why Are Hydro Flask Water Bottles Durable?
The durability of Hydro Flask water bottles owes to two factors: the thick stainless steel the bottle uses and the anti-rust and anti-scratch powder coating it applies.
Compared with other water bottles in the market, both the external wall and the internal wall of a Hydro Flask water bottle are thickened, enabling customers to enjoy better insulation capability and a longer service life. Furthermore, the durable and colorful powder coating offers extra shielding and nice appearance.
Can the Quality of Hydro Flask Water Bottles Be Surpassed?
When it comes to this question, the answer is definitely “yes”. In fact, there are about 8 Chinese water bottle manufacturers including KingStar that can produce water bottles of the same or even more outstanding quality. In order to achieve that, water bottle manufacturers are supposed to do the following things:
- Material: Manufacturers should choose optimal food grade stainless steel SUS304 as the body material.
- Thickness: Outer wall and inner wall should be thicker than 0.5mm
- Technology: It is a must to have an insulation technology by sealing the air and thickening the stainless steel walls.
- Manufacturing Process: Every water bottle manufacturing process such as welding, powder coating and vacuuming should be performed strictly and precisely.
- R&D team: A great research and development team plays a significant role in the improvement of water bottles’ quality and performance.
- Quality Control team: In order to surpass the quality of Hydro Flask water bottles, a quality control team is also indispensable.
Are The Hydro Flask Water Bottles Made In China?
It has been well proved that 95% of the world’ s water bottle comes from China, and all Hydro Flask water bottles are made in China. It won’t take you too much time to find the “Made in China” lettering on the bottom of a Hydro Flask water bottle.