Powder coating become more and more popular these days for insulated stainless steel sport bottles. There are several advantages of powder coating layer. Anti-slip, durable and colorful. As a leading vacuum insulated stainless steel water bottle manufacturer, KingStar has rich experience in powder coating process. To help you understand the process and make decision when you are not sure to choose spray painting or powder coating, in the following, we would be showing you the details of powder coating process of stainless steel bottles.
Powder Coating Process Principle
The powder coating is sprayed onto the surface of the insulated stainless steel bottle body by electrostatic powder spraying equipment (static spray machine). Under the action of static electricity, the powder will be uniformly adsorbed on the surface of the bottle body to form a powder coating; The coating is cured by high-temperature baking and flattening, and becomes the final coating with different effects (the different kinds of effects of powder coating); the spraying effect is superior to the painting process in terms of mechanical strength, adhesion, corrosion resistance and aging resistance. The cost is also under the same effect of painting.
Process flow
Grinding –> Alkali Washing 1 –> Water Washing 1 –> Water Washing 2 –> Acid Washing –> Water Washing 3 –> Phosphating 1 –> Surface Optimization –> Phosphating 2 –> Washing 4 –> Doing Putty –> Drying –> Polishing –> Blowing Off Dust –> Spraying Plastic Powder –> Blow off Excess Plastic Powder –> High Temperature Drying –> Cooling –> Decorating –> Testing/Checking
Main Process Steps:
Pre-treatment
- Purpose: remove the oil stain, dust and rust on the surface of the insulated water bottle, and form a “phosphating layer” on the surface of the insulated water bottle that is corrosion-resistant and can increase the adhesion of the spray coating.
- Main process steps: degreasing, descaling, phosphating, passivation. After the pretreatment of the insulated bottle, not only the surface has no oil, rust and dust, but also a gray and white shiny surface produces a uniform and rough gray phosphating film which is not easy to rust, which can prevent and increase the spray coating adhesion
- Related equipment: pre-treatment tank (concrete trough, the number is equal to the number of pre-treatment steps);
- Related materials (chemicals): sulfuric acid (H2SO3), hydrochloric acid (HCl), soda ash (Na2CO3), acid degreaser, Phosphating solution, passivation solution.
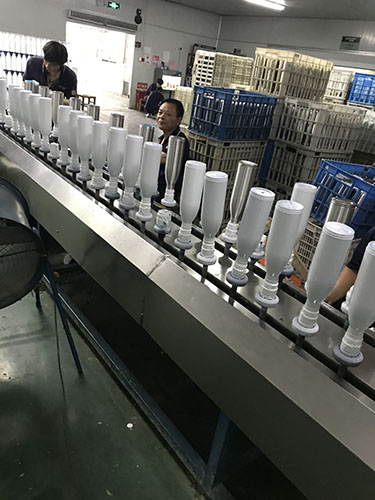
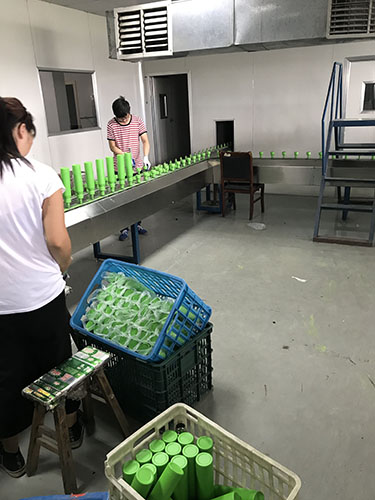
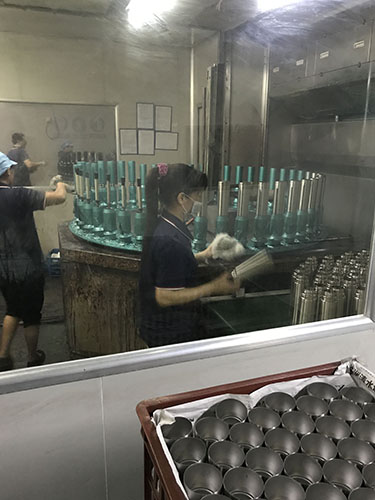
Electrostatic powder spraying
1. Purpose: the powder coating is evenly sprayed onto the surface of the insulated bottle, special bottle (including locations that are prone to electrostatic shielding) should be finished with a high-performance electrostatic spray machine.
2. Bottles Preparation: the parts that do not need to be coated should be covered.
3. Equipment Preparation
Electrostatic generator: Check if the static generator power supply is normal and the voltage output is normal.
Electrostatic generator parameter check: Electrostatic voltage: 30-70KV
Powder bucket: Check whether the powder is in suspension.
Spray gun: Check whether it is cleaned. No residual powder is allowed. Debug the spray gun: Turn on the static generator, and the powder is adjusted by the intake air. The air pressure starts from zero and gradually increases to see if the powder is even.
Powder tube: Check whether it is cleaned. No residual powder is allowed.
Powder pump: Check whether it is cleaned. No residual powder is allowed.
Air compressor: Check if the compressor works normally and the air pressure meets the requirements.
Air pressure: 0.6-0.8MPa
Powder supply: 150-250g/min (adjustable)
Compressed air freeze dryer: Check whether it works.
Gas path oil-water separation device: Check whether it works. Check whether the oil discharge and drainage devices are working properly.
4. Powder coating function checking
Check if the powder is normal, voltage, air pressure, and equipment operation is normal.
5. Powder Coating: The distance between the spray gun and the insulated water bottle is 10-20cm. The spray gun can be closer to the insulated water bottle when spraying the weld bead and the part that is not easy to be powdered. When spraying, the spray gun moves back and forth to the surface of the bottle horizontally or vertically, and the speed should be uniform. The thickness of the dust at the concealed part or the weld bead should be slightly thicker.
High-temperature drying
- Purpose: The powder coating on the surface of the insulated bottle is heated to the specified temperature and kept for a corresponding time to melt, level and solidify, so as to obtain the desired surface effect of the vacuum insulated stainless steel bottle.
- Process steps: Push the sprayed bottle into the high temperature drying / curing oven, heat to a predetermined temperature (typically 185 degrees), and keep the corresponding time (15 minutes);
- Tips: heating and control system (including electric heating, fuel, gas, coal and other heating methods) + insulation box = high temperature drying oven.
The drying tunnel should be cleaned regularly and the temperature is even. According to the plastic powder curing requirements, the temperature is adjusted to 180 ° C -230 ° C, the flow rate of the insulated stainless steel bottle in the drying tunnel is adjusted according to the plastic powder curing time.
- Related equipment: high temperature drying oven / curing oven. (Parameters that need automatic control: temperature, holding time, heating method can be electric heating, fuel heating, gas heating, coal heating, etc., can be flexibly selected according to the energy situation in your area).
- Related materials: High temperature curing ovens (or ovens, ovens) capable of controlling temperature and holding time within a reasonable range.
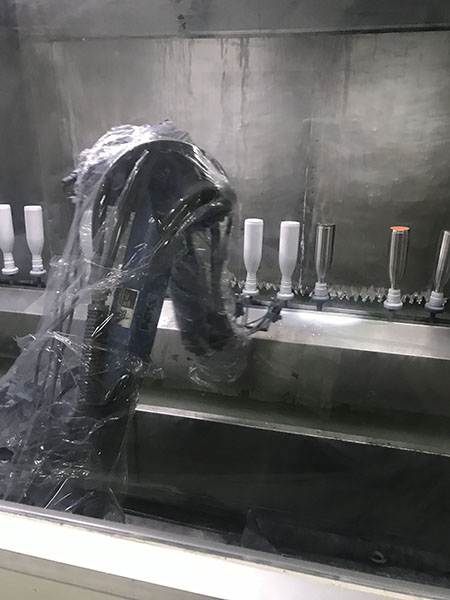
Decorating
- Purposes: to make the insulated bottle after electrostatic spraying to achieve a special appearance such as: a variety of wood grain, pattern, lightening and so on.
- Process steps: cover light; transfer and other processing techniques.
Testing/Checking
1. Coating thickness: 60-100um, uniform thickness.
2. Coating hardness: 2H
3. Coating strength:
a. Fix the test bottle so that it does not shake when it is impacted.
b. The impactor is vertically erected on the tested part of the device to be tested. The head is inlaid with a Φ12mm steel ball and a heavy outward hammer with an outer diameter of Φ17mm and a total weight of 100g. It is free to be 1m in the impactor with an inner diameter of Φ19. Falling vertically, the coating of the test piece is subjected to a falling impact.
c. Remove the impactor and the coating on the impact site should be free of flaking and cracking. The impact test is repeated three times in the same position on the same test piece at a distance of not less than 100 mm. If one item fails, the piece is judged to be unqualified.
4. Adhesion:
a. On the coated surface of the test piece, 10 parallel lines parallel to each other with a pitch of 1 mm were drawn with steel needles to a depth of the base metal.
b. Then, 10 lines parallel to this line with a pitch of 1 mm are scribed, and the scribe lines should be performed in the same direction.
c. At the intersection of the lines, the coating should not be peeled or peeled off.
d. In case of dispute, the magnifying glass with a magnification of not less than 2 times should be used for review and judgment.
To know How Vacuum Insulated Bottles Are Made and read complete vacuum insulated stainless steel bottle manufacturing process, please go to: https://www.waterbottle.tech/manufacturing-process-of-vacuum-insulated-stainless-steel-bottles/
KingStar is a professional vacuum insulated water bottle manufacturer. We focus on developing and manufacturing high quality vacuum insulated water bottles, flasks, tumblers and mugs that aim at keeping liquids hot or cold for long hours. You want to source private label water bottles? Just contact us.